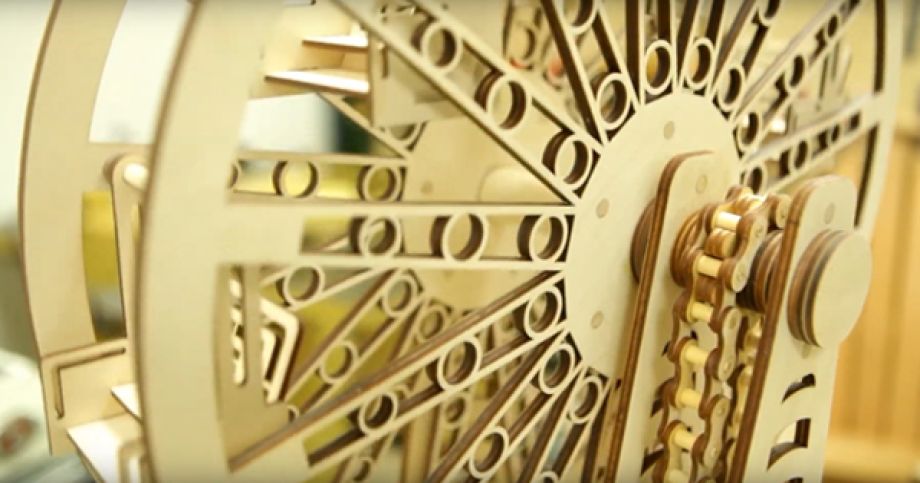
Doug Green
Hobbyist-turned-business owner incorporates Epilog Laser System into dream workshop
Doug Green’s love for woodworking began in high school in his hometown of Austin, TX. Though his professional career didn’t move in that direction, Doug’s natural ability, coupled with the right equipment helped him successfully turn his hobby into a job where he could bring his woodworking creations from concept to reality.
“I’m mainly a hobbyist, working in wood and metal, along with laser design and engraving,” Doug tells us. “I’m fortunate to have a full wood and metal working shop – my dream shop, in fact – and I started my company, Express Laser Service in January 2009″.
In a laser system, I was looking for a large bed size. In a manufacturer I was looking for the best after-sale service. I have found both with Epilog and Engraving Concepts. They’re both first class in service after the sale. I’m three years into this adventure, and after going to all the shows and talking to other vendors I would still buy an Epilog again and again.
Doug Green
Having a fascination with lasers for nearly 20 years, Doug recalls the first time he was introduced to the technology. “A little over 20 years ago I bought some handmade wooden pens that were laser engraved with the name of the company I was working for at the time,” Doug said. “Ever since then I wondered ‘how’d they do that?’. A little over three years ago I was at a woodworking show in Austin, TX, where I was introduced to Engraving Concepts, and they were demonstrating an Epilog Laser system in their booth. A friend of mine had a wooden pen in his pocket and they laser engraved his name on it – that was all it took. I knew I had to have a laser! At the time I had no idea how it would change things in my shop.”
Shortly after Doug saw the Epilog demonstration, he began the process of finding the right laser system for his needs.
“In a laser system, I was looking for a large bed size. In a manufacturer I was looking for the best after-sale service. I have found both with Epilog and Engraving Concepts. They’re both first class in service after the sale. I’m three years into this adventure, and after going to all the shows and talking to other vendors I would still buy an Epilog again and again.”
At first Doug used the laser system primarily to cut out patterns and prototypes. “I use a lot of quarter-inch medium-density fiberboard (MDF) and the laser cuts through it like butter,” Doug said.
“I think my learning curve hit an apex last year when I saw a map of a lake that had two layers to give a topographical effect. I made one myself, using a photo of a map of our local lake. It took two days to create a design I was happy with, but after some test runs and multiple edits, I was off and running. My maps, which I create with the laser, are three layers: the land around the lake, the lake itself that is painted blue, and then the river bed painted a darker blue. I have made maps of different lakes, as well as the Texas coastline,” Doug tells us.
Doug is a perfect example of how certain projects can turn into other profitable ideas. “From the lake maps, I developed a two-layer clock, and have made more than 100 of them – only 20 have been the same.”
Always one to tackle new projects and explore new ideas, Doug tells us his work as of late has been in of the model-making nature. “It began with a (working) model wooden pipe wrench. Then I made an all wood chain and wood sprockets. And since then I have been racking my brain to think of something to make that would use the chain. After many months I came up with an all wood Ferris wheel.”
Doug tells us the Ferris wheel project took a total of about 30 to 40 hours and has been well worth the effort. “I just love drawing and creating something so intricate – the sky is the limit and the laser can engrave or cut anything you can draw.
“In fact both the Ferris Wheel and the wood chain were made mostly with the laser. The only other tools I used were a small miter box, small backsaw, random orbital sander and a wood lathe, and that was only to drill the eighth-inch hole in the center of the quarter-inch dowel for the pin and roller for the chain,” Doug told us. (See materials list at end of story.)
“Like I said before, the sky is the limit with the laser, and who knows what I will make next? I recently made a bridge based off someone else’s drawing, and my next project will be making a model of our local bridge.”
Material make up of Ferris wheel:
- The Ferris wheel is all wood from the ground up.
- 1/8” Birch plywood, and in most cases is sandwiched together to form 1/4”.
- Doug also used 1” and 1/4” birch dowels and wood glue.
- Under the floor in the box is a four-RPM gear motor, four bolts, washers and nuts, two wood screws and four springs – the rest of the structure is entirely made from wood.
- Doug drew and made the wood chain for the Ferris wheel. It has 1/8” birch dowels to form the pins and 1/4” birch dowels to form the roller of the chain.