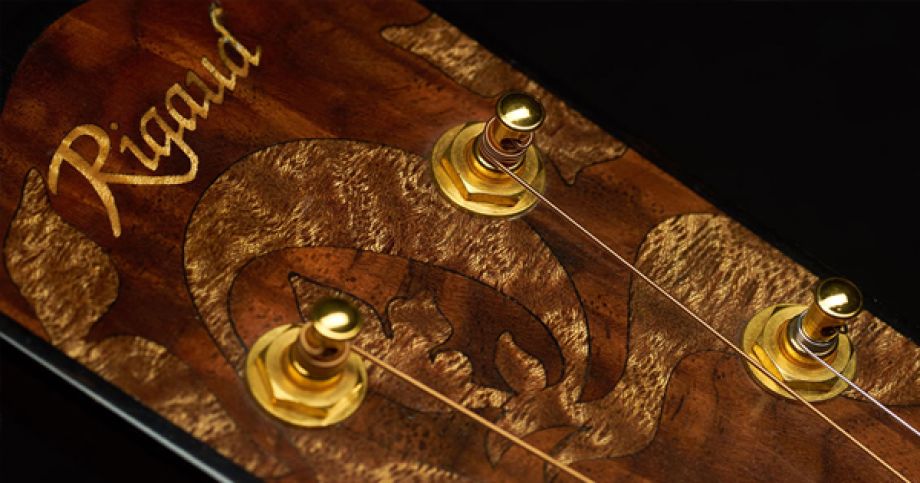
Rigaud Guitars
Epilog Laser increases instrument customization capabilities for Rigaud Guitars
Bob Rigaud has had an extensive career in the music industry. A skilled luthier (maker of stringed musical instruments), Bob graduated from the Roberto-Venn Luthiery school in Phoenix in the mid 1970s and later returned to his Alma Matter to teach. In 1979 he headed east to Greensboro, NC, where he established a home-based shop specializing in the restoration of vintage instruments while also maintaining a volume repair business for local music stores and school systems.
Over the years, Bob has provided guitars and repair services for numerous well-known musicians, including Nokie Edwards of The Ventures, John Hiatt, John Fogerty, and Bo Diddley. In 2005 he scaled back his repair business to concentrate on design and development of his own instruments.
Today Rigaud Guitars employs the Epilog for a vast array of manufacturing tasks. Beside performing astonishing inlays, engraving and the manufacturing of essential guitar components, we also manufacture a variety of non-musical items including handmade jewelry boxes, guitar pick boxes that employ an integrated temperature and humidity gauge, pet urns, signage, scrimshaws for knife handles and gunstocks and many specialized acrylic templates, jigs and tools that are employed in the manufacture of fine stringed instruments
Bob Rigaud
Today Rigaud, owner of RG Music & Rigaud Guitars, only accepts repairs and restorations on a limited number of instruments that he finds interesting, mostly rare instruments that might otherwise be lost.
In 2006 Bob Marsh brought Rigaud a rare Martin guitar for repairs and restoration. At the time Marsh worked for Epilog customer, Senator USA, LLC, a promotional products company. From his work with Senator’s two Epilog systems, Marsh recommended that Epilog systems could significantly benefit Rigaud’s operation. Marsh encouraged Rigaud to see the systems for himself, and after Rigaud visited Senator and saw their Epilogs in action he became intrigued with the possibility of doing custom guitar work with one of the machines.
“We needed a machine that could accurately engrave and cut a variety of materials ranging from hardwoods to bone, plastic and laminates,” Marsh said. “After considering cost, customer service and my existing knowledge of the lasers, Rigaud ordered a 60-watt Epilog Helix and a short time later hired me on to assist in running the equipment for custom instrument work.”
In addition to stunning inlays, Marsh tells us their Epilog is utilized in a number of ways. “Today Rigaud Guitars employs the Epilog for a vast array of manufacturing tasks. Beside performing astonishing inlays, engraving and the manufacturing of essential guitar components, we also manufacture a variety of non-musical items including handmade jewelry boxes, guitar pick boxes that employ an integrated temperature and humidity gauge, pet urns, signage, scrimshaws for knife handles and gunstocks and many specialized acrylic templates, jigs and tools that are employed in the manufacture of fine stringed instruments.”
Bob Rigaud is a gifted artisan who works diligently on his craft. Each of his guitars are similar in size and shape; however, each is unique and built entirely to the customer’s requests and specifications according to the particular style of music for which it will be used. He also manufactures a limited number of carved electric guitars that demand endless hours of hand carving, the finest woods and electronics and the most elaborate inlays and decoration. With the exception of strings, tuning keys and the neck truss rod, each instrument produced at Rigaud Guitars is made from raw materials. In an age where mass-produced instruments are the rule, Rigaud Guitars are the exception. Since incorporating the Epilog Laser system, Marsh tells us the business has expanded.
“We’ve definitely grown with the use of the Epilog. While each guitar takes hundreds of hours to produce, in terms of customization of instruments, the variety of products we can offer and the streamlining of processes and tooling, we are well ahead of the curve that existed five years ago. We’re utilizing technology to create beautiful pieces of art,” Marsh said. “I often wonder if Epilog lasers existed in the time of Stradivarius, Orville Gibson or Christian Friedrich Martin would they have used them? I’d bet big money they’d be all over the Epilogs in a heartbeat.”
To learn more about Riguad Guitars, visit rgmusic.com. To contact Bob Rigaud or Bob Marsh, email info@rgmusic.com.